From lecture halls to workshop floors: the journey of one mechanical engineering capstone project
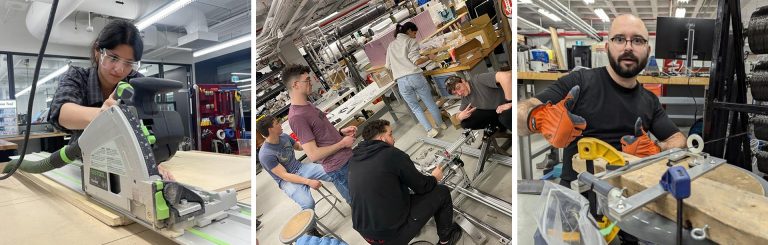
Milo Claydon is an undergraduate mechanical engineering student at Concordia. Claydon worked alongside his capstone team members: Najwa Boumelhem, Andrea Devulder, Joshua Belley, Dimitri Condax and Jonathan Krusemer.
Engineering students at Concordia have the opportunity to undertake Capstone Engineering Design Projects in their final year. For ours, my team and I designed and built a carbon fibre filament winding machine for Space Concordia. That’s a mouthful, so let me explain what it does and why it is important.
Composite materials are often used in aerospace as they are both strong and lightweight. Carbon fibre offers excellent tensile strength. The Rocketry Division at Space Concordia used to rely on volunteers to lay carbon fibre sheets, painted in epoxy, by hand over a rocket engine mandrel. This took 10 students several long days to complete. These volunteers required extensive training, and as new students came in and older ones graduated it was difficult to maintain a qualified team.
Also, this hand-layup method introduced wrinkles or weak points between sheets, which meant more material had to be used to compensate, and the rocket would be heavier. They needed a better way of making these aerospace grade composite parts — that’s where we came in.
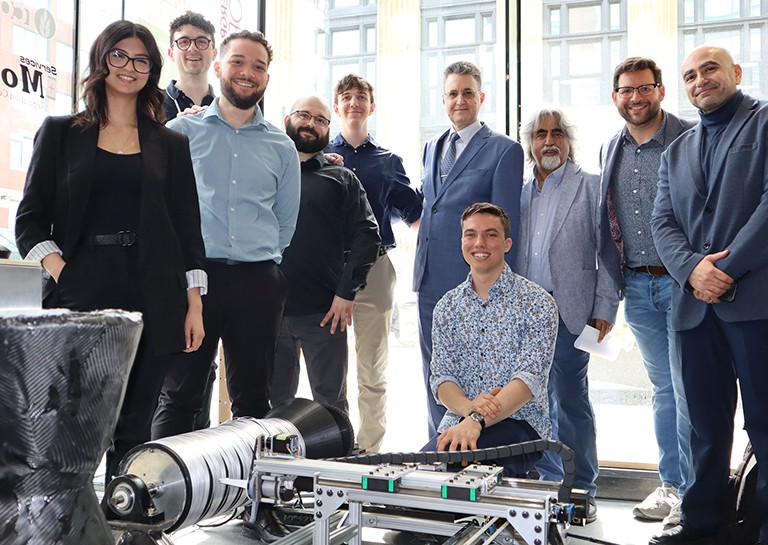
Automating a complex process
Our goal was to help automate this manual and time-consuming process. Space Concordia initially suggested modifying an existing off-the-shelf winder, which is typically used to create parts about the diameter of a pop can. This machine was never intended to handle the 150-kilogram, six-feet-long, 18-inch diameter mandrels we needed to wind. We quickly realized we would need to build this thing from the ground up. We replaced stubby drill chucks with massive, welded frames, little plastic wheels with linear rails and flimsy belts with ball screws.
The filament winding machine we built works similarly to a 3D printer. That means it can make the rocket parts pretty much by itself (with some supervision, of course). It uses stepper motors to move in controlled directions and wraps strands of carbon fibre onto a spinning mould. As the mandrel rotates, carbon fibre strands are drawn through a resin bath and wrapped around the mould in a continuous pattern. This allows for uniform coverage, precise fibre placement and reliable results.
What once took 10 people multiple days can now be done by two operators in under two hours. It’s not just faster, it’s significantly more consistent. The machine is also modular, which means it can be adapted to wind other parts like combustion chambers, fuel tanks, nose cones and fuselages. For a student-run organization with limited time and resources, this flexibility is a major advantage.
Our machine can wind fibres at specific angles and with specific tensions. This lets the design team use fewer fibres and control the quantity of resin being deposited, reducing the mass and the cost of the parts being made.
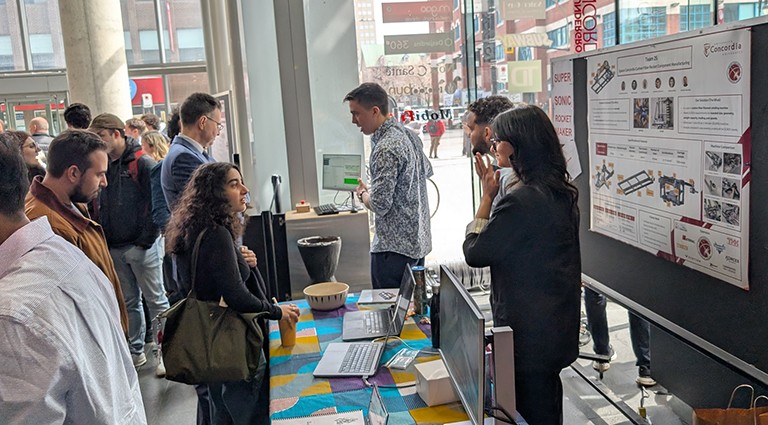
Applying what we learned in class (and learning what we didn't)
One of the most valuable lessons from this project came from comparing our classroom experience with the challenges of building something real.
In lectures, we learn the theory behind structural design, stress calculations, control systems and material selection. That knowledge helped us understand what to model, simulate and research. It gave us a place to start. But the moment you step into a workshop, you begin to realize how much more there is to learn. Nothing works exactly as it would theoretically. We learned that a good engineer relies on intuition to anticipate how real-world implementations will deviate from theoretical models.
We encountered problems that would never appear on a problem set. Parts didn’t fit the way they did in our design, welded parts warped, electronics had noise and nothing was truly the exact dimension it was meant to be. At one point, we spent days debugging a set of limit switches that turned out not to work just because the wires were too long. Wrapping them in tinfoil got our machine working.
These aren’t the kinds of solutions that come from a textbook. They come from building, testing, failing and trying again. This project showed us what real-world engineering looks like. It’s messy, creative and deeply satisfying.
Advice to future engineers
To any student considering engineering or preparing for a capstone project, here’s what I’ve learned: Concordia offers incredible opportunities, but you have to look for them. If you take initiative, there are countless chances to work on meaningful projects, learn from experienced professors and build something that matters. We owe the success of this project to the incredible facilities and technicians, particularly in the Engineering Design and Manufacturing Lab and the Gina Cody School Makerspace.
From your first year, pay attention to the people you work well with. Keep in touch with the classmates who challenge and motivate you. A capstone project is only as good as the team behind it. If you build that team with care, you’ll get to the end of your project not just with a final deliverable, but with lasting friendships and valuable experience.
And always stay curious. Everyone has something to teach you if you’re willing to learn.
Find out more about Concordia’s Gina Cody School of Engineering and Computer Science.